While monitoring the 24/7 Internet news cycle it seems not an hour goes by without another 'news' story about driverless cars, usually showing someone behind the controls grinning from ear-to-ear with their hands off the steering wheel like they're riding a roller coaster. The fact that these systems are merely an advanced form of cruise control never seems to penetrate the reality distortion field generated by the hype machine pushing these stories.
History
Speed regulating cruise control (originally named “Auto-pilot”) was first put into a production car almost 60 years ago. Lane Keeping Assist features were first introduced almost 25 years ago. A Honda version of LKAS that provided 80% of steering torque to keep the car in the lane on highways has been on the market since 2003.
Similarly autonomous cruise control with auto brake features was also first introduced 25 years ago and there are now 15+ auto brands offering these systems. Even cars that park themselves have been on-sale for over a decade. (2003 Toyota Prius) Yet as we're about to hit 2017 these functions still has enough novelty value that some media types have branded them 'robot cars'??
Google
Self driving car (SDC) hype really leapt off the Richter scale when Google acquired a startup called 510 systems in 2008. A small team of UC Berkeley students with DARPA Challenge experience built a robotized Toyota Prius called “PriBot” for a TV show pizza delivery stunt.
It's clear that choosing a Toyota Prius to become the first road legal SDC was a strictly functional decision. The mass market adaption of hybrid and electric vehicle brake regeneration has played a large role in enabling self driving cars. The two features that allow relatively easy implementation of robotic control in production cars are 1) electric power steering 2) brake-by-wire regenerative braking. In conjunction with by-wire throttle, these systems allow direct control of steering, acceleration & moderate braking via low-voltage electronic signals that can be generated in software. This is why all SDC's are either hybrid or electric cars.
What is less clear is how well self driving cars handle emergency situations. Despite hybrids and EVs primarily using regen braking to the extent that brake pads now last the life of the vehicle, anti-lock brakes and stability control functions are still part of the legacy friction brake system that requires human muscle input to activate. The work-around has been to restrict Google prototype testing speeds to 25 mph (40 km/h) and requiring a safety drivers onboard at all times.
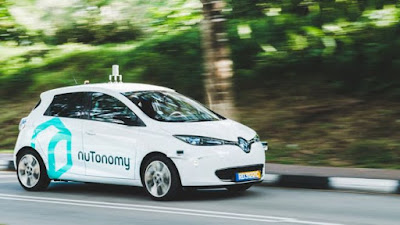
Despite the fact nine US states have passed legislation to allow public road testing of 'driverless' cars, by some estimates, Google cars are unable to use about 99% of US roads. Aside from their inability to drive in anything but perfect weather conditions, the cars do not carry the computing horsepower to process all the required data in real-time so the car’s exact route must be extensively mapped. Data from multiple passes by a special sensor vehicle must be pored over, meter by meter, by both computers and humans before any SDC can test a new route. It’s vastly more effort than what’s needed for Google Maps.
While there are half a dozen public 'trials' of self-driving cars/shuttles active around the world , they are either on private roads/campuses or if on public roads, they run in very geographically limited areas. None of them are strictly speaking 'driverless' as they all have human 'safety' drivers.
Safety
The original goal for Google's SDC program, as stated by the “godfather” of self-driving Sebastian Thrun, was to promote safety. Most definitely a laudable goal, but is a map localising cruise control really the best solution to reduce 1 million road deaths and 50 million serious injuries every year?
Real world evidence is starting to suggest, maybe not! A long read by Tim Harford published by The Guardian makes the case that too much automation increases driver in-attention to the point that responding to emergency situations becomes more dangerous, a situation known as the automation paradox.
While governments around the world are cracking down on driver distractions like texting while driving, with the UK now suggesting that offenders could face a life sentence, self-driving/auto-pilot systems actively promote in-attention by lulling drivers into a false sense of security.
The fact is that while SDC systems are designed to replace the driver, they do nothing to improve functional vehicle safety. SDC's still has the same mandatory mechanical friction brake based anti-lock and stability control systems as any other car on the road. A self-driving system has the same three basic controls to operate a vehicle as a human driver, yet with the introduction of electric vehicles the potential is there to develop augmented digital by-wire control systems that can bring commercial aviation levels of safety to the automotive world.
Fly-by-wire was developed 50 years ago for aerospace during the Apollo program. Augmented fly-by-wire electronic control systems aid and protect aircraft in flight via 'control laws' that provide flight envelope protection, a human machine interface (HMI) that prevents a pilot from making control commands that would force the aircraft to exceed its structural and aerodynamic operating limits. These augmented HMI systems are standard equipment on commercial aircraft and today’s impressive safety and reliability statistics are a testimony to the advanced technology represented in fly-by-wire digital flight control systems. Yet despite the ever increasing level of electronics in ICE powered vehicles, they are still primarily direct control mechanical systems with some limited power assistance.
Electric Vehicles
The introduction of electric powertrains opens the opportunity for augmented drive-by-wire control via primarily solid-state electric powertrains. Replacing mechanical friction brakes with electromagnetic braking by incorporating an electric motor for each individual wheel, either in-board or in-wheel, establishes a direct digital connection that allows precise control of vehicle dynamics and takes human muscle strength out of the loop. This allows a rules based augmentation system to compensate for a drivers lack of knowledge and/or skill while providing a 'guardian angel' to protect drivers from exceeding a vehicles dynamic limits, or in some cases can assist them in reaching those limits.

In 1992, Daimler-Benz performed a study that utilised its driving simulator in Berlin, which revealed some striking data about simulated panic stops and crashes. In the study, more than 90% of the drivers failed to apply enough pressure to the brakes when faced with emergency situations. This is co-incidentally the same figure the SDC industry often quotes, “some 90% of motor vehicle crashes are caused by human error.”
Based on the Daimler study it seems clear that despite the fact drivers react to emergencies, their lack of training/familiarity with either the braking effort required and/or the capability of the vehicles braking system is the cause of the majority of road accidents. In 1996 Mercedes-Benz introduced yet another extension to hydraulic brakes called Emergency Brake Assist which compensates for 1) human leg muscle strength still being required to operate a modern automobile 2) the "buzzing" feedback and sinking brake pedal during ABS operation.
So does a hybrid brake-by-wire system qualify as an advance that removes human leg muscles from the loop? For moderate brake applications yes, but because brake regeneration is limited by battery charge rates to 50-60 kw max, under emergency braking the car defaults back to the legacy hydraulic friction brake system with it's plethora of add-on systems like ABS, ESC, EBA, EBD etc that, while power assisted, still requires leg muscle strength.
I have previously discussed how hydraulic friction brakes on hybrid and electric vehicles are effectively redundant, yet because of regen limits a Google self-driving Toyota Prius would only be able to perform moderate braking under computer control, requiring human leg-muscle input for emergency braking, which seems to defeat the advertised purpose of the program?
A drive-by-wire quad motor electric powertrain could provide a machine to machine (M2M) / human to machine interface (HMI) that would require no more leg effort to execute an emergency stop from any speed than operating a throttle pedal, while also incorporating all mandatory safety features in software to be executed via brake-mode torque vectoring all while keeping the vehicle within it's safe dynamic envelope. A drive-by-wire powertrain would provide a platform for map localising algorithms and various 3D sensor hardware to work together in a similar fashion to aircraft auto-pilot and rules based augmented fly-by-wire in commercial aviation. Drive-by-wire would provide a certifiable advanced computer control system to monitor and step-in to assist drivers to improve road safety while we're all waiting the next 10-20-30 years for consumer ready self-driving cars.