In part 2 of this series (Part 1) we'll take a closer look at electromagnetic braking as a replacement for mechanical friction brakes in hybrid and electric passenger cars.
Electromagnetic braking is very well established in industrial applications. From 400 tonne mine haul trucks to 300 km/h Bullet trains, electromagnetic 'friction' is used to slow these high performance vehicles with industrial strength reliability, so why shouldn't it also be used on comparatively light weight private passenger vehicles ?
Lets take a look at a few of the more familiar applications of electromagnetic braking. Japan's Shinkansen high speed rail network has the best safety record on the planet: beating conventional trains, automobiles and flying. Over the Shinkansen's 50-plus year history, carrying over 10 billion passengers, there have been zero fatality / injury since 1964. Clearly many factors contribute to this but obviously the train braking system plays an important role, especially given the maximum operating speed is 320 km/h (200 mph).
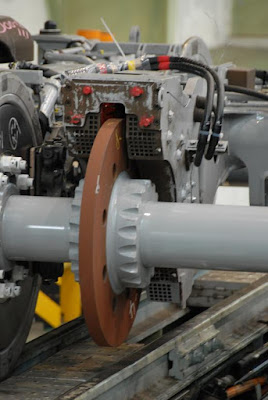
Bullet trains uses electricity to brake up to 640 tonnes down from 300 km/h at a controlled and predictable deceleration rate. Since 1984 all Shinkansen trains have used axial flux eddy current disc brakes (pictured above). These work along the same lines as an eddy current dyno where a steel brake rotor has electromagnets facing it, that when energised, induce eddy currents in the rotor which generates electromagnetic friction that converts the trains kinetic energy into heat.
With the only moving part being the rotor and no wear and tear from mechanical friction, eddy current brakes have proved incredibly reliable and no doubt contribute to the 100% safety record achieved by the Shinkansen rail system. Since 2007 next generation Bullet trains have moved to regenerative braking that uses the main traction motors which helps increase overall system efficiency.
Another very large vehicle that uses electromagnetic brakes is the 400 t class Liebherr T282B Mine haul truck. with a maximum operating weight of almost 600 tonnes, the T282B has no mechanical connection between the monster 90 liter V20 twin turbo diesel engine and the rear wheels.
Instead it takes advantage of high efficiency and maintenance free diesel-electric locomotive technology. Siemens provide two AC induction motors for the rear axle, engine mounted generator and the solid state computer controlled power inverters that are proven over millions of operating hours in trains. The main service brake electric retarders can slow the truck to a stand-still and provide precise speed control on descent using built in cruise control which works in both drive and retard modes.
The electric retarders can apply over 6,000 hp (4,489 Kw) worth of braking effort (the Diesel ICE maximum output is 'only' 3650 hp (2700 Kw). Like the Bullet train there is no battery storage system on-board so the regenerated energy is not stored for later use but is converted to heat via a stainless steel resistor grid in a systems called dynamic braking.
If ultra-reliable electromagnetic braking of 600 tonne vehicles hasn't convinced you then surely this last example will. Strictly speaking this is called magnetic braking as the source is permanent magnets, yet it is just as impressive.
Drop Tower amusement park rides feature up to 400 feet (120 m) towers with a carriage capable of taking up to 40 passenger aloft. Once 30 stories off the ground, the 25 tonne carriage is dropped and free-falls back down the tower reaching speeds of 105 km/h. Built by Swiss firm Intamin, the eddy current magnetic brakes pull the falling riders up at 2.5G from 100 to 0 km/h within 100 feet.
To put that into perspective, a Tesla Model S brakes from 100 to 0 km/h in 113 feet, weighs only 2.5 tonne and moves parallel to the ground, not hurtling head-first towards it.
The common threat between all the above braking applications is that mechanical friction brakes would simply not be capable of reliably doing the job. While these electric braking systems convert kinetic energy into heat, as do hydraulic friction brakes, using electromagnetic friction offers a non-contact method of braking that virtually eliminates maintenance and therefore reliability issues.
In the previous post we've seen evidence that hydro-mechanical friction brakes on hybrids and EVs have become redundant legacy systems primarily still required on vehicles because they provide mandatory safety systems. In order to allow electromagnetic braking to functionally replace systems like ABS & ESC not only do we need each wheel to have an electric motor to drive / brake each wheel independently, but also additional electromagnetic braking strategies other then just regeneration feeding kinetic energy into a battery pack.
Currently in hybrid and electric vehicles only a fraction of the electric motors full power is used for braking. For example, a Chevy Volt has 115 kw of electric motor power available for acceleration but only 60 kw for braking. Even a Tesla Model S with over 500 kw for acceleration is limited to 60 Kw maximum brake regeneration. The primary reason for this is battery cell charge limits. Most lithium ion batteries have asymmetric charge & discharge curves.
In order to allow full electric motor power to be applied in brake mode, alternative energy discharge methods are required. As we have seen in the examples provided above, there are several options from dynamic to eddy current braking and/or the addition of supercapacitors in parallel with the battery pack. With an electric motor for each wheel and full motor power available for braking, modulating the motors independently to perform anti-lock, stability control, emergency brake assist, automatic emergency braking and torque vectoring becomes a software project.